Atelier Bretagne è un subappaltatore della fabbrica di automobili PSA e ha sede nella periferia di Rennes. L’azienda opera 7 giorni su 7 e 24 ore su 24, dovendo seguire il ritmo degli ordinativi effettuati dalla committenza.
IL PROBLEMA
Nel tempo il continuo passaggio dei carrelli elevatori aveva reso il sottofondo inadatto a sostenere i carichi a cui era sottoposto e il pavimento a lastre risultava danneggiato.
Le esigenze del cliente
Per i responsabili dell’azienda era assolutamente impensabile sospendere l’attività lavorativa poiché i costi di un’eventuale fermo dei lavori sarebbero risultati molto superiori a quelli necessari per demolire e rifare la pavimentazione.
Perché è stata scelta la soluzione Uretek:
- Rapidità
attenta pianificazione e programmazione dei tempi di esecuzione che permettevano di realizzare l’opera in tempi relativamente brevi; - Costi competitivi
- Non invasività
l’intervento proposto da Uretek non richiedeva l’interruzione della normale attività lavorativa, non avrebbe sporcato l’area né prodotto scarti di lavorazione; - Monitoraggio continuo del lavoro
le attività sarebbero state sottoposte a controllo laser in tempo reale da personale altamente qualificato; - Applicazione della tecnologia esclusiva Uretek Floor Lift®
che inietta nel terreno una speciale resina espandente ad alta pressione di rigonfiamento che compatta il terreno e stabilizza le strutture; - Attenzione all’ambiente
la miscelazione fuori terra delle resine Uretek® genera un prodotto finale inerte, che non rilascia eluati nel terreno e nelle eventuali falde presenti.
LA SOLUZIONE
Si trattava di compattare un sottofondo di 7.000 mq di pavimentazione senza generare sollevamenti indesiderati del pavimento e senza interferire con i ritmi produttivi dell’azienda. Abbiamo dunque applicato la tecnologia Uretek Floor Lift®, che ci ha permesso di saturare i vuoti iniettando negli stessi la resina espandente Uretek in grado di sollevare i sottofondi fino a 20-30 cm e oltre, correggendo pendenze ed eliminando dislivelli. Abbiamo così ottenuto il rafforzamento del sottofondo e ripristinato il contatto con la pavimentazione.
Per verificare il successo del nostro intervento abbiamo impiegato comparatori sensibili al centesimo di millimetro. La stabilizzazione dei 7.000 mq di pavimento ha richiesto 35 giorni lavorativi e l’utilizzo di circa 20 tonnellate di resina espandente Uretek.
L'INTERVENTO NEL DETTAGLIO
Le fasi operative
Poiché non si poteva programmare un fermo delle attività lavorative, abbiamo pianificato attentamente i tempi di esecuzione per ciascuna fase dell’intervento, così da ridurre al minimo l’interferenza con l’attività produttiva dell’azienda. Attraverso le rilevazioni effettuate, abbiamo verificato che nella zona attorno ai giunti di dilatazione la pressione esercitata dai carichi era estremamente elevata. Tenendo conto di questa osservazione, abbiamo realizzato la foratura della pavimentazione seguendo una maglia con un foro ogni mq di pavimento e aumentando la densità dei fori attorno ai giunti di dilatazione. L’intervento ha richiesto l’esecuzione di una serie di fori di 12 mm di diametro nel pavimento e la posa di cannule metalliche attraverso le quali iniettare la resina Uretek nel sottofondo della pavimentazione. Durante le iniezioni abbiamo posizionato dei livelli laser per controllare che non si verificassero sollevamenti indesiderati del pavimento.
Monitoraggio
Dopo ogni iniezione, abbiamo eseguito il controllo dei risultati tramite un comparatore sensibile a movimenti di 1/100 di millimetro. In pratica, su ogni zona di pavimento trattata, facevamo passare un carrello elevatore carico e misuravamo l’abbassamento. I risultati ottenuti sono stati nettamente migliori della tolleranza inizialmente richiesta pari a 20/100 di millimetro.
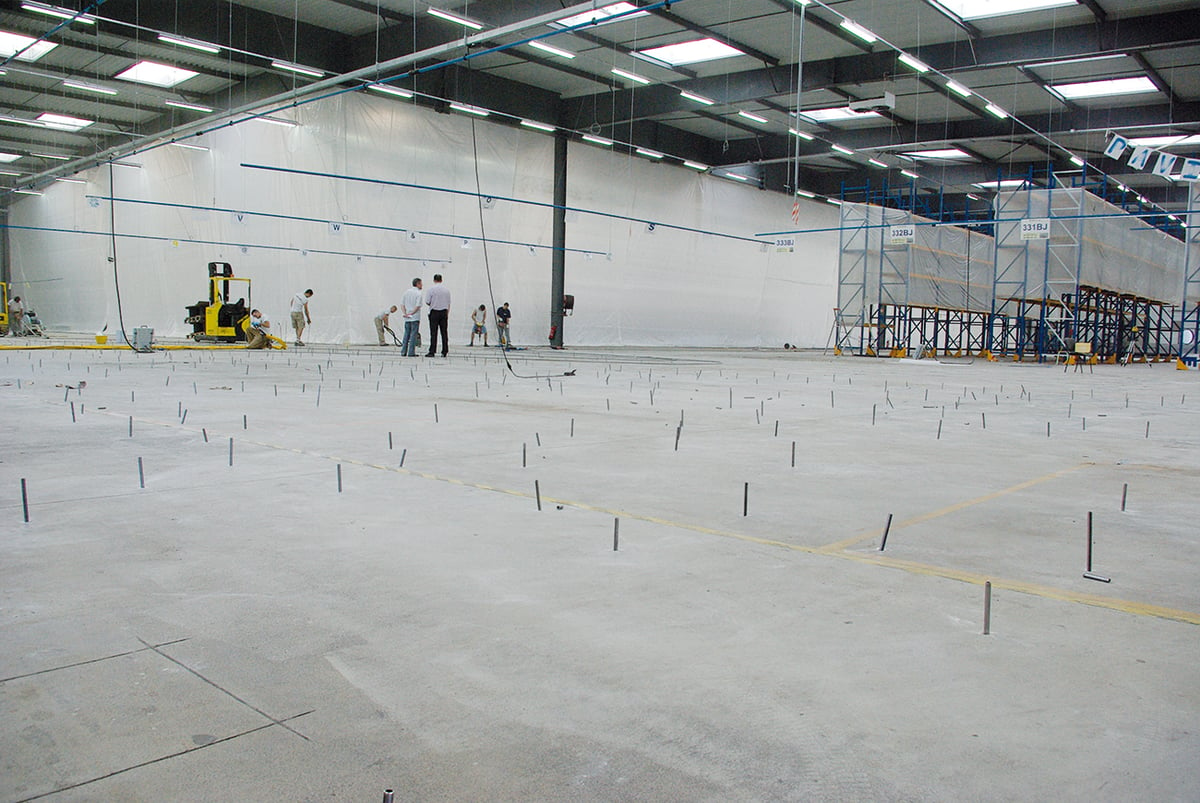
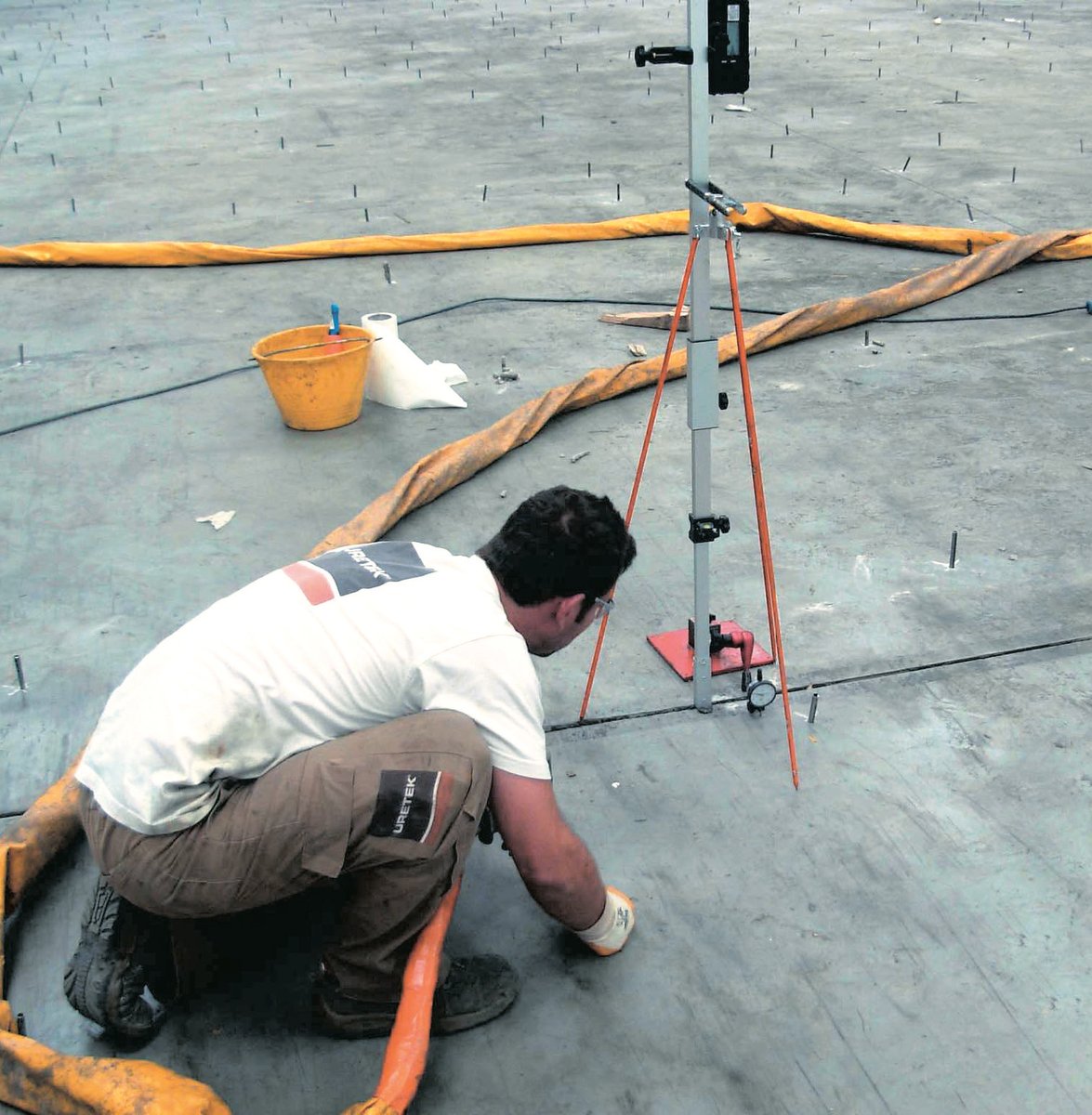
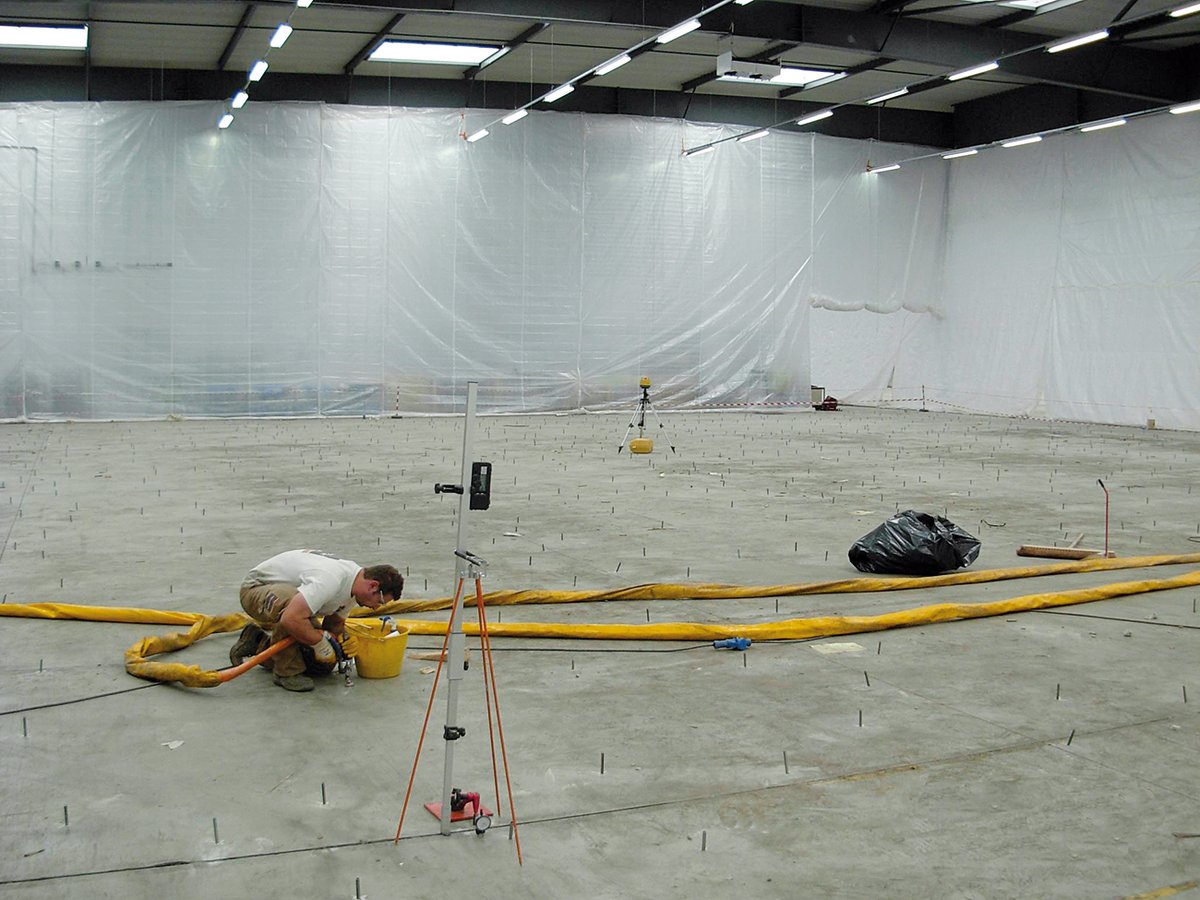
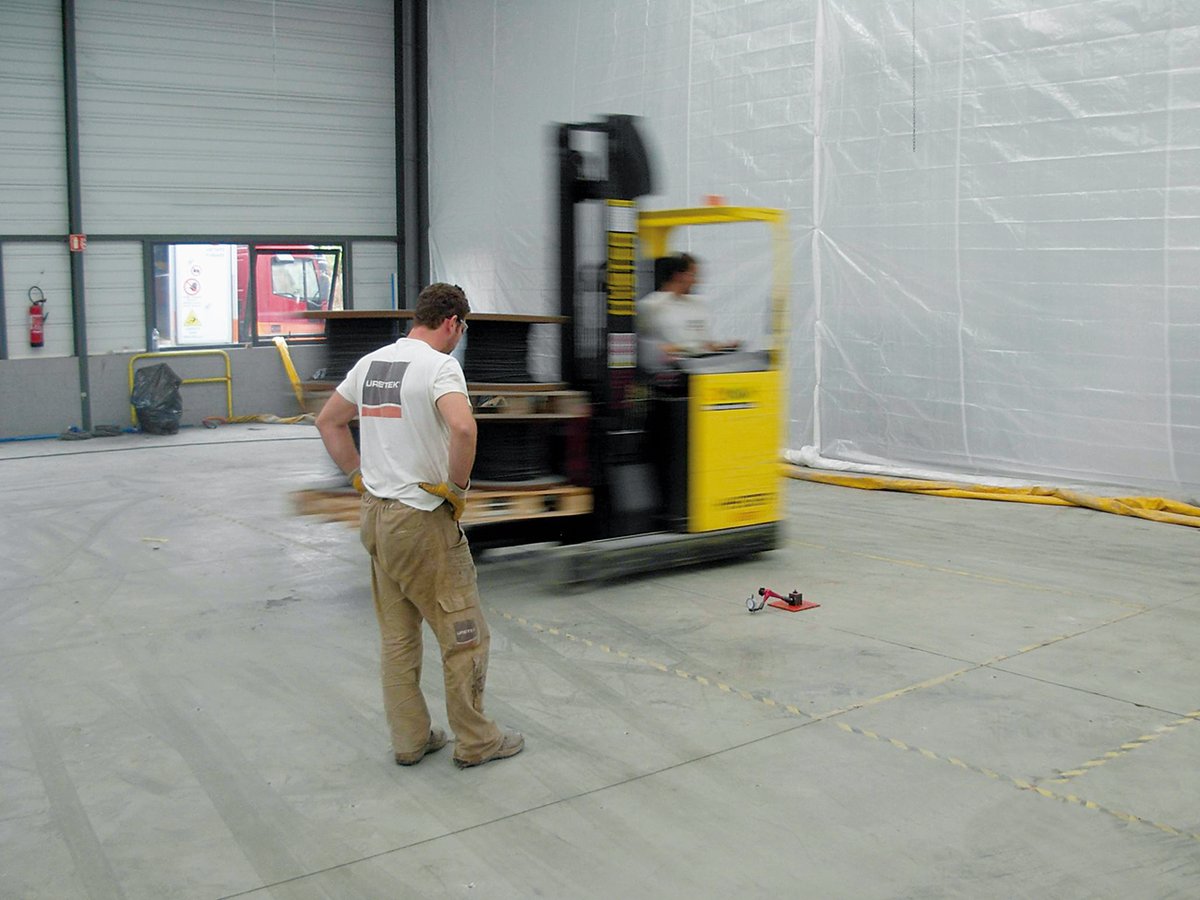